You are here
Putting Humanoid Robots to Work
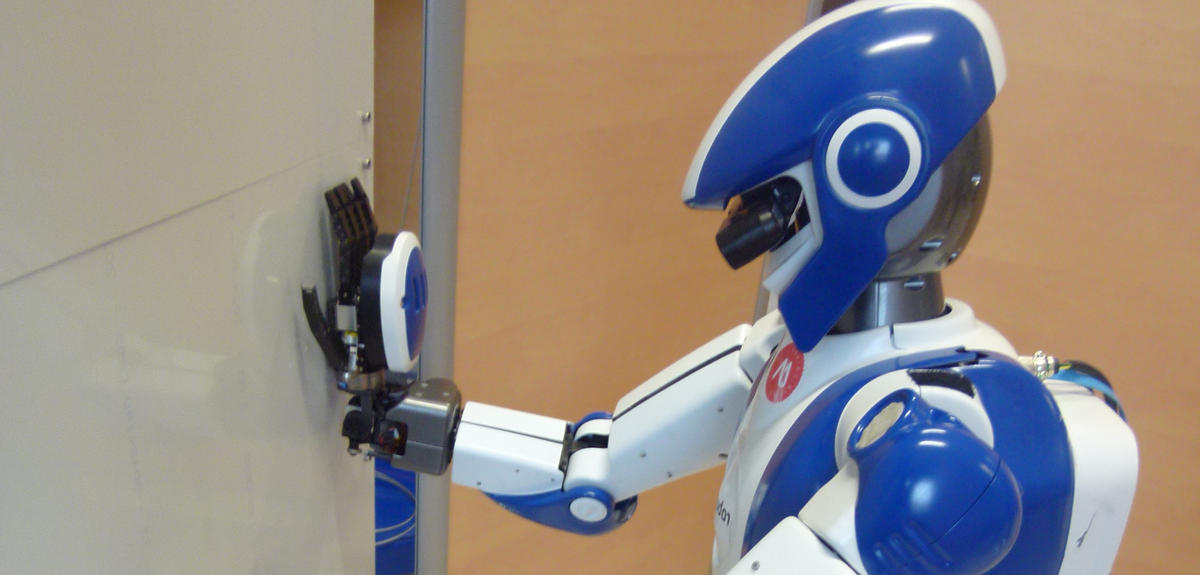
A new Joint Research Program1 was just launched between the Joint Robotics Laboratory (JRL)2—which has brought together the CNRS and the AIST3 for more than a decade—and Airbus Group, with the goal of developing humanoid robots specifically designed for aviation manufacturing. This program is the culmination of two years of interaction that revealed to both parties the strong potential for development in this field.
Faster, better, stronger?
“Given the unique nature of aviation assembly and the specialized character of the tasks involved, Airbus Group has very well-defined needs,” explains Abderrahmane Kheddar, the director of the JRL, which is at the heart of the program. “For instance, robots must be capable of navigating through narrow spaces such as fuselages, and executing complex tasks from a variety of positions. In short, the manufacturer needs humanoid robots that can make human movements such as kneeling or leaning, and that can perform more sophisticated functions, such as screwing or torqueing,” adds Adrien Escande, the leader of the joint research program.
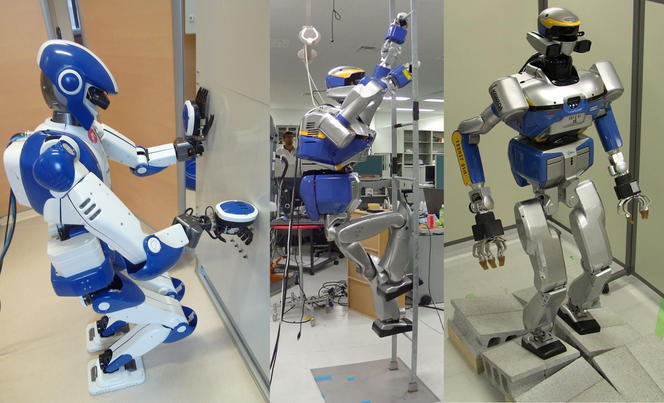
Fortunately, since the creation of the JRL in 2004, Kheddar and his team have made such advanced functionalities an emerging reality rather than the stuff of science fiction or the far-off future. “By combining Japanese expertise in hardware and robotics along with advanced French knowledge of mathematics and algorithms, we made encouraging initial progress in fields such as robot design and haptics, or tactile perception,” continues Kheddar. “We are now building on these achievements to develop multi-contact locomotion, which enables humanoid robots to move using not just their feet, but also other body parts such as elbows, knees, and hands, as a human would when crawling.”
Command and control
As coordinators of the COMANOID European research project,4 JRL researchers have already helped tailor multi-contact locomotion for the aviation industry, which needs humanoid robots that can safely move around assembly plants without endangering human workers, the planes, or themselves. They then proceeded to have these robots carry out simple tasks, such as delivering an object to a specific location. As part of this new JRL, the team is expanding these basics by working on more intricate movements that require improvement in two key areas: robot control and planning. “To illustrate what this means, try to imagine a rock-climber,” suggests Adrien Escande. “To take the next step on a rock face, they must think ahead by identifying possible foot and handholds, and by deciding which movements to make, and in what sequence. This is the planning function. Then there is the control function, which enables the climber to adapt their movements in real-time based on uncalculated events, such as a slip or a gust of wind. We are currently using numerical optimization techniques and advanced algorithms to improve capacity in both of these areas.”
For instance, in order to open a panel at knee level, a robot can prepare the execution of the task by determining where to kneel, how to grasp the handle, and where to place its hand against the wall for support. Unlike these preparatory calculations, which can take up to a few minutes, control function analysis requires immediate reactions. To help a human worker move a heavy object, a humanoid robot must be able to anticipate and react to the worker’s movements in real-time, which requires computing speeds on the order of milliseconds rather than minutes.
To do this and much more, researchers proceed by modeling robotic perception and behavior. Every analytical decision or maneuver is conceived of as a mathematical “problem,” which is translated into an equation and then “solved” by algorithms developed by the scientists. In the operation mentioned above, opening the panel would involve calculations for balance (while kneeling), distance (to leave room for the opening panel), and counter-balancing force (to lean forward against the wall so as not to fall backwards). Such micro-level adjustments are made by humans unconsciously, but must be programmed for robots. Other algorithms have been developed for bipedal locomotion, fall control, and contact force distribution.
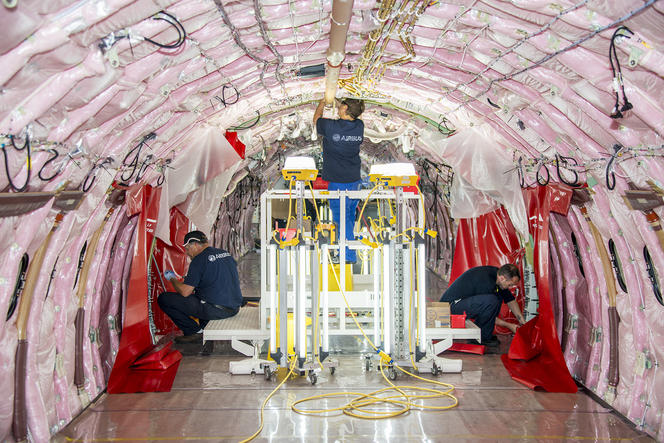
Watch and learn
Efforts are also underway to improve robot-learning capacity. This is done by teaching the machines to teach themselves by searching for information in databases or on the Internet. As part of another European research project called RoboHow, JRL researchers helped robots learn new tasks—such as loading paper into a printer, or baking a pizza—by reading instructions on the Web and storing them in their knowledge base. The instructions are supplemented with learning videos, digitally-analyzed human demonstrations, and imitation learning. These various sources are then integrated by the robot in order to carry out the task. The goal, of course, is to develop more independent robots that can expand their range of knowledge and skills.
The robots being developed for Airbus Group’s aviation plants could later be adapted for its helicopter and aerospace activities. They could also be tailored for the needs of other industries with large and complex assembly sites, such as train or ship builders, who need mobile rather than stationary robots, and ones that can carry out a wide rather than a limited range of tasks.
“It should be very clear that these humanoids are not intended to replace workers, but rather to offer them better working conditions by freeing them from chores that are physically-taxing or that involve contact with pollutants,” concludes Kheddar. “This enables workers to focus on the more skilled and value-added aspects of their activities. In other words, these robots are sophisticated tools intended to assist them as part of a synergistic human-robot collaboration.”
- 1. “Whole-body manipulation for humanoid robots in constraint environments,” CNRS-AIST-AIRBUS, Joint Research Program, http://wbmice.cnrs.fr/
- 2. CNRS-AIST Joint Robotics Laboratory (JRL), UMI3218/RL.
- 3. National Institute of Advanced Industrial Science and Technology (AIST).
- 4. Multi-Contact Collaborative Humanoids in Aircraft Manufacturing (COMANOID). http://www.comanoid.eu.
Explore more
Author
Arby Gharibian is a writer, translator, and independent researcher in social sciences, art, and literature .