You are here
Materials: Stretching the Limits
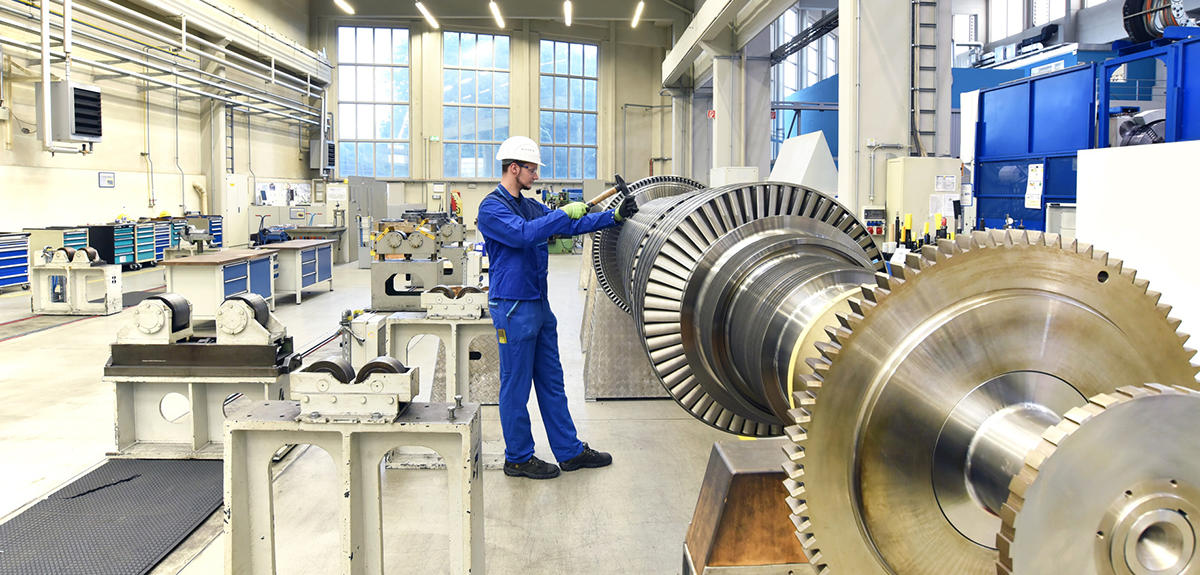
Our lives already rely on vast panoplies of technological equipment, and as scientific advances continue to push new generations of devices to perform ever more exacting tasks, a few uncertainties remain. Are the materials we use fit for enduring harsh conditions like radiation, extreme temperatures or pressures, deformation or vibrations? And even so, how can we improve materials to have longer lifespans?
Key for industry
Industry, for example, calls on a number of arduous processes—involving heat, chemicals or reshaping—which potentially strain the materials that make up the equipment. This is all the more the case when the overriding aim is to maximize yield, as exemplified by the nuclear-power industry. “To produce the best possible energy yield, nuclear-reaction procedures expose equipment to searing temperatures, extremely high pressure, corrosive turbine-turning water vapor, as well as irradiation,” explains Jean-Yves Cavaillé, INSA Lyon researcher and French director of ELyTMaX,1 a new Franco-Japanese international joint unit (UMI)2 dedicated to assessing existing materials and finding new solutions, namely for industry, biomedicine and energy conversion.
“It’s not just exposure to a single element which is hard on equipment, but their joint action all at once, making the conditions both extreme and complex,” he adds. Researchers are thus seeking strategies to boost the durability of materials facing multiple strains. In the case of the metal alloys used in nuclear-reactor equipment, the new unit studies “the development of extremely pure materials—alloys whose exact composition is very precisely determined—because impurities are what weakens alloys.”
More generally, the robustness of industrial equipment can be enhanced by coatings that protect the various parts of machinery from wear or corrosion. One method currently being explored is the “cold spray” technique, whereby “powder particles of matter like metals or polymers are sprayed at high velocity onto a surface to be protected,” explains Kazuhiro Ogawa, Japanese director of ELyTMaX. Slammed onto the surface at high speed, the particles are deformed—pretty much flattened—making them bond more tightly with the surface and the other sprayed particles. The result is a harder, denser coating. “Here, we subject particles to extreme conditions precisely to fight against extreme conditions,” enthuses Nicolas Mary, a cold-spray specialist also from INSA Lyon. For now, cold spray is at a “fairly empirical stage with researchers testing its possibilities via experimentation,” but the team at ELyTMaX aims to deepen theoretical understanding of its mechanisms in order to enhance its industrial potential.
Biological strain
Extreme conditions present a challenge for an increasing number of fields, not just large-scale industrial equipment. At the other end of the scale are customized biomaterials inserted into the human body as bone substitutes or prosthetics. “When a person with a prosthesis jumps or does sports,” says Cavaillé, “the pressure on the device is enormous.” Indeed, artificial body parts—usually made of ceramics, metals or polymers—must tolerate a high level of movement in any number of directions, just as their deterioration may be sped up by the physical or chemical properties of their environment, such as “the corrosiveness of saline solution used for certain prosthetics.” Something else that needs to be factored in when choosing materials is the fact that living tissue follows a natural ageing process, and implants in contact with it must be able to adapt to this change. ELyTMaX researchers will thus focus on developing materials that strike this fine balance between solidity and flexibility. Going one step further, what if stress, vibrations, or movement gave materials a boost—literally?
Jolts of power
Indeed, the most surprising research at ELyTMaX may involve turning rough or “extreme” conditions into a resource. And it all has to do with energy conversion, using piezoelectric materials that are capable of creating electricity when deformed. One ELyTMaX team is looking into alternatives to classic piezoelectric ceramics—namely far more flexible and low-cost polymers—to develop smart systems that transform equipment vibrations into usable energy. In the aviation industry, for example, the energy from jolts and tremors in flying aircraft—currently lost—could be harvested to power multiple sensors embedded throughout the plane for the in-flight monitoring of its various components. A major advantage of such a self-powering monitoring system would be its independence from the plane’s engine-driven electrical system, cutting the need for complex wiring. Yet to get this type of energy-conversion system to work, materials often need to be exposed to another extreme element—very high voltages which radically reduce the materials’ lifespan. In this regard, the researcher admits that “we’re still far off from being able to make them last long.” Another challenge is that scientists have yet to develop systems small but powerful enough to be viably integrated into various plane structures.
From assessment to design
Energy conversion, biomaterials and industry thus form the priority topics of the new unit, which places modeling and simulation (M&S) at the heart of its strategy, without neglecting experimental aspects. On the one hand, these techniques allow scientists to address a common concern for any material, namely “knowing how long it will last before it becomes dangerous,” says Gael Sebald, ELyTMax team member from INSA Lyon. To find out, researchers first identify the mechanisms that govern the material’s behavior, then use M&S to trace their evolution over time and assess the material’s life expectancy and performance-degradation rate. But this approach can also be used upstream to optimize the design of future ones. The team at ELyTMaX follows a “materials by design” approach for creating materials with improved properties. “Instead of taking a whole range of materials and chancing upon the right one, we decide which properties we need, then use deduction to work out the best combination of materials for meeting our technical specifications,” explains Cavaillé.
Stronger together
ELyTMaX is the latest incarnation of a longstanding association between Tohoku University and several institutions in Lyon.3 Already, in the last 30 plus years, the Franco-Japanese alliance has given rise to joint seminars, workshops, research programs, double-degree arrangements, the opening of liaison offices in both Lyon and Sendai in 2004, as well as the creation, in 2008, of the ELyTLab, an international associated laboratory (LIA)4 promoting joint research in five key areas.5 ELyTMaX provides a new physical structure in Sendai with an unprecedented emphasis on extreme conditions, offering a bridge between engineering science at Lyon and at Tohoku. “It is a natural progression of the partners’ work on complementary topics in practically every domain—in fact our topics exist because of this complementarity with research on one side bouncing off research on the other,” conclude the researchers.
- 1. Engineering Science Lyon – Tohoku for Materials and Systems under Extreme Conditions (CNRS / Institut National des Sciences Appliquées Lyon / Ecole Centrale de Lyon / Université de Lyon I / Tohoku University). Launched on October 4, 2016, it is based at Tohoku University in Sendai (Japan).
- 2. Unité mixte internationale: a full-fledged lab gathering researchers from the CNRS (along with the Université de Lyon in the case of ELyTMax) and a partner institution (here, Tohoku University) on one site.
- 3. Namely the Université de Lyon, the Institut National des Sciences Appliquées Lyon and the Ecole Centrale de Lyon.
- 4. Laboratoire international associé: a wall-less CNRS structure pooling the human / material resources of a CNRS lab and an overseas lab.
- 5. Biosciences & Engineering; Durability, Reliability in Energy and Transportation; Nano & Micro Scale Materials & Devices; Flow Dynamics, Heat Transfers and Microfluidics; Tribology.
Author
As well as contributing to the CNRSNews, Fui Lee Luk is a freelance translator for various publishing houses and websites. She has a PhD in French literature (Paris III / University of Sydney).